Detailed Underwater Inspections and Reports
Did you receive a notice from the City of Detroit requiring an inspection of your seawall? Give us a call at 224-619-4307 and we can assist you.
Many properties located on or near water include seawalls or revetments – sloping-front or vertical-front structures that run parallel to the shore. Seawalls are an important and potentially expensive feature of a waterfront property.
Completing a seawall inspection during due diligence and prior to purchasing a property can identify problems that may lead to large expenditures in the future.
Inspecting a seawall on a routine basis after purchasing a property is an important part of a preventive maintenance program.
To learn more about our seawall inspection services, or to see a sample report, call us at 224-619-4307.
How do seawalls work?
The main forces on a seawall can be separated into the hydraulic responses of the waves and the structural response of the seawall. The main loads and structural responses include the wave forces exerted on the wall, as well as the forces applied by the backfill soil and water pore pressure.
What is included in our detailed seawall inspections?
Seawall monitoring is typically divided between condition monitoring and performance monitoring.
Condition monitoring is the basis for the implementation of a successful preventive maintenance program. Seawall condition monitoring involves at least visual inspection of the structure, and in some cases, the inspection is augmented with measurements meant to quantify the current structure condition relative to the baseline condition.
Performance monitoring of seawalls mainly focuses on the assessment of the principal function of preventing or alleviating overtopping and flooding of the land and the structures behind the seawall due to storm surge and waves.
Our visual inspection of a seawall, both above and underwater, will identify some of the following information pertaining to the wall:
Seawall composition
Seawall toe and crest levels
Structural integrity of the seawall
·Wave overtopping
Beach scour
Water table levels
We utilize a variety of techniques for seawall inspections:
Visual inspection from land
Visual inspection from above or below the water line
Ultrasonic thickness readings of metal walls both above and below the water line
Acoustic imaging
We use the latest specialty technology for our seawall inspections:
Ground Penetrating Radar (GPR): The steel tie backs of a seawall must be fully evaluated to determine the efficacy of the wall. Steel tie backs are typically installed during the initial construction and help support the weight loads applied to the wall. When conducting our inspection of a seawall, we use what is called ground penetrating radar, or GPR, to locate the steel tie backs and accurately assess their current condition. Properly evaluating the condition of the tie backs is a vital piece of the inspection because if the tie backs fail, movement of the wall, and ultimately wall failure may occur.
LITE tool, from Pile Dynamics: If you have a steel wall, knowing the length of the steel pile in the ground can be useful for verifying design criteria of older walls and confirming the ability of the wall to support new loads. We use the LITE tool from Pile Dynamics to effectively evaluate the length of the existing steel piles including: steel sheet piles, H-piles, pipe piles, cased drilled shafts, and highly reinforced drilled shafts. The LITE tool uses the inductive field method for correctly determining the length of a steel pile.
Examples of our work:
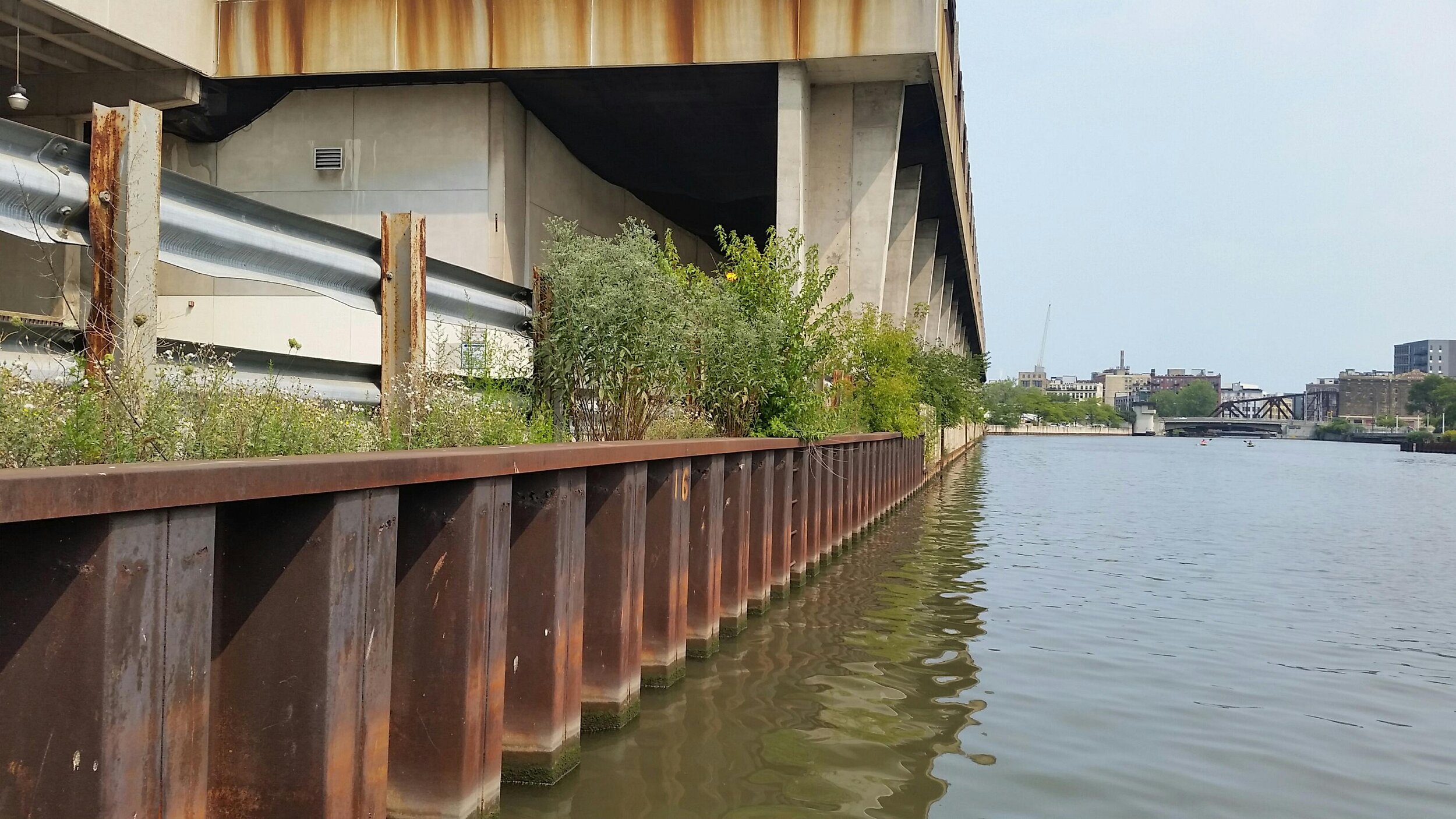
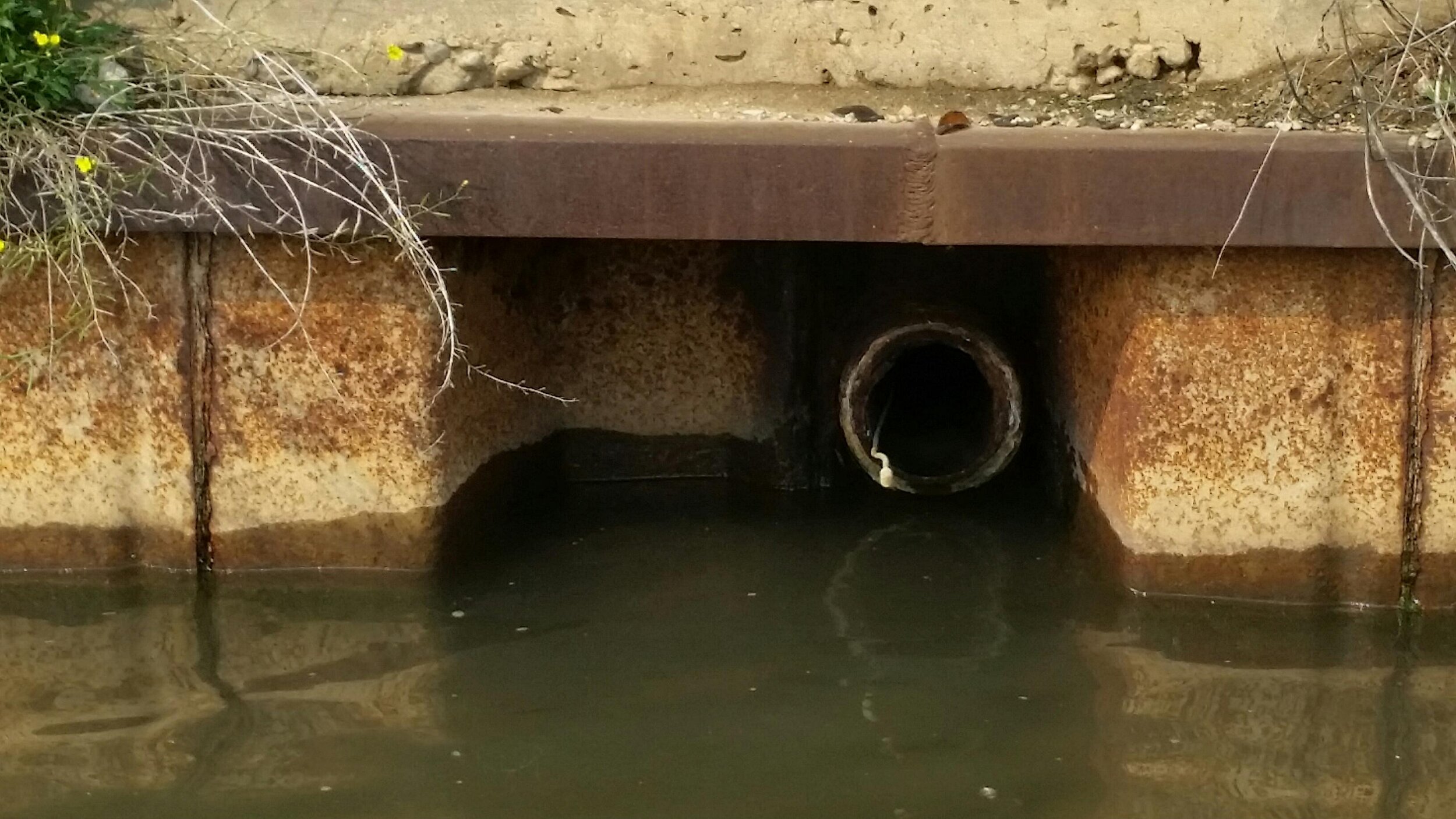
Additional resources on seawall inspection:
We perform inspections in general accordance with industry standards including:
FHWA report FHWA-DP-80-1 “Underwater Inspection of Bridges”, June 2010
ASCE Manual 101 “Underwater Investigations Standard Practice Manual” 2001
AASHTO Manual for the Condition Evaluation of Bridges
Inspection services are generally classified into levels based on the scope of work:
Level I: Visual / tactile inspection
Level II: Detailed inspection with partial cleaning of biofouling to inspect the structure beneath the growth
Level III: Highly detailed inspection with Non-Destructive Testing (NDT) or Partially Destructive Testing (PDT)
Other resources you can consult include:
United Facilities Criteria (UFC ) #4-150-07 Maintenance and Operation: Maintenance of WaterfrontFacilities
New York City Economic Development Corporation Waterfront Facilities Maintenance Management System Inspection Guidelines Manual
The Repair, Evaluation, Maintenance and Rehabilitation (REMR) Notebook, U.S. Army Corps of Engineers
American Institute of Marine Underwriters (AIMU) Docks, Bulkheads, and Wharfs Paper
Service areas
Our engineers are licensed to perform seawall inspections in the following states: Florida, Georgia, Illinois, Indiana, Iowa, Kentucky, Louisiana, Michigan, Minnesota, North Carolina, Ohio, South Carolina, Texas, and Wisconsin.